Wäscheförderer
Gewerbliche Wäschereien verarbeiten typischerweise über 500.000 lose Wäschestücke pro Woche. Um dies effizient zu erledigen, ist Automatisierung unerlässlich. Förderbänder bilden das Rückgrat automatisierter Transportsysteme in Wäschereien. Sie transportieren die einzelnen Wäschestücke zwischen den Schmutzwäscheannahmebereichen, durch die Reinigung und schließlich zur Verpackung und zum Versand an den Verbraucher.
Zu den typischen Förderbandanwendungen in Wäschereien zählen:
- Sortieren schmutziger Wäsche
- Indexierende Stufenförderer zum Beladen von CBW-Waschmaschinen mit Lasten von 50–100 kg
- Kuchenförderer
- Wäschesortierbänder und -plattformen
- Trocknerbeschickungswagen und Abtransportbänder
- Ein- und Auslaufbänder für Schrumpfverpackungsmaschinen
Viele Wäschereien arbeiten an bestehenden Standorten mit vielen Altgeräten. Eine Herausforderung für die Automatisierung besteht darin, Platz für die Installation von Förderbändern zu finden. Alle Amber-Förderbänder werden für den individuellen Einsatzzweck entwickelt und gebaut und lassen sich daher durch Anpassung von Länge, Breite und Höhe des Bandes problemlos an die Anforderungen vor Ort anpassen.
- Pulverbeschichtet, Weichstahl, Betten mit Volants aus Edelstahl oder Pulverbeschichtung
- Glatte Innenflächen
- Spaltfreie Innenflächen
- Gesäumte Kanten um Volants
- Endlosbänder
- Fingerschutz an der Walzenkrone und robust
- Horizontalförderer bevorzugt unmittelbar vor Abwurfübergabestellen
- Erhöhen Sie die Fördergeschwindigkeit beim Übergang von einem Band auf ein anderes
- Keine Belastung über den Seiten der Volants
- Die Fallhöhe zwischen den Förderbändern darf nicht geringer sein als die Höhe der Volant des Zuführbandes.
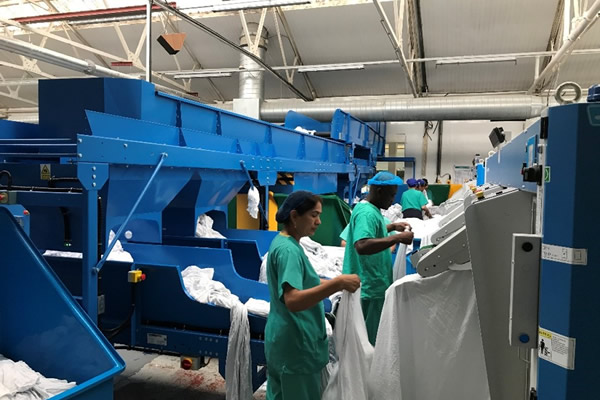
Anwendungen für Förderbänder in Wäschereien
Gewerbliche Wäschereien verarbeiten typischerweise über 500.000 lose Wäschestücke pro Woche. Um dies effizient zu erledigen, ist Automatisierung unerlässlich. Förderbänder bilden das Rückgrat automatisierter Transportsysteme in Wäschereien. Sie transportieren die einzelnen Wäschestücke zwischen den Schmutzwäsche-Eingangsbereichen, durch die Waschprozesse und weiter zur Verpackung und schließlich zum Versand der gereinigten Wäsche an den Verbraucher.
Im Wareneingang werden Bandförderer eingesetzt, um Schmutzwäsche schnell von den Lieferwagen zu den Sortier- oder Waschbereichen zu transportieren. Je nach Wäscherei kann auch das Sortieren auf den Eingangsförderern erfolgen. Nach dem Waschen kann die saubere Wäsche zu einem „Kuchen“ gepresst werden, um überschüssiges Wasser zu entfernen. Anschließend werden die Förderer erneut eingesetzt, um den Kuchen in einen Sortierbereich oder direkt zu Trocknern zu befördern. Nach dem Trocknen wird die Wäsche über weitere Förderer zu den Wäscheteams transportiert, die die Mangel- und Faltmaschinen beschicken.
Nach dem Bügeln und Falten kann die Wäsche über ein letztes Förderband zur Versandabteilung transportiert werden, wo sie für die Rückgabe an den Verbraucher gelagert wird. Um die Effizienz der Wäscheförderbänder zu verbessern, werden häufig zusätzliche Fördergeräte wie Aufzüge, Hebezeuge und Verfahrwagen eingesetzt. Der Wäscheprozess kann über 120 Stunden pro Woche und 52 Wochen im Jahr laufen. Daher sind in jeder Phase zuverlässige, robuste und widerstandsfähige Geräte erforderlich. Hier zeichnen sich die Wäscheförderbänder von Amber durch ihre wäschereispezifische Konstruktion aus.
Viele Wäschereien arbeiten an veralteten Standorten mit viel Altgeräten. Eine Herausforderung für die Automatisierung besteht darin, Platz für die Installation von Förderbändern zu finden. Alle Amber-Förderbänder werden für den individuellen Einsatzzweck entwickelt und gebaut und lassen sich daher durch Anpassung von Länge, Breite und Höhe des Bandes problemlos an die Anforderungen vor Ort anpassen.
Die in Wäschereien verarbeitete lose Wäsche stellt besondere Herausforderungen an die Automatisierung und insbesondere an Förderbänder dar, denen durch eine gute Konstruktion entgegengewirkt werden kann. Das Hängenbleiben der Wäsche entlang eines Förderbands ist das größte potenzielle Problem und muss durch glatte, durchgehende und möglichst lückenlose Innenflächen verhindert werden. Lücken, die sich in Laufrichtung verjüngen, sind unbedingt zu vermeiden, da sich die Wäsche darin verfängt und festklemmt.
Der Wäschetransport in einer Wäscherei erfolgt üblicherweise über mehrere miteinander verbundene Förderbänder. An den Kreuzungspunkten der Förderbänder kann es zu einem Hängenbleiben kommen, da die Wäsche von einem Förderband wegrollt und vom anderen aufgenommen wird. Um das Hängenbleiben an den Verbindungsstellen zu reduzieren, sollte die Geschwindigkeit des Abfuhrförderbandes deutlich höher sein als die des Zufuhrförderbandes. Dieser Geschwindigkeitsunterschied ist besonders wichtig bei Förderbändern, die von geneigter zu horizontaler Ausrichtung wechseln, da die Wäsche dort in den Spalt zwischen den Rollen gerät.
Die Verwendung von Rollen mit kleinem Durchmesser, z. B. 60 mm, am Anfang und Ende von Förderbändern ist vorteilhaft, um die Größe des V-Abstands zwischen den Rollen zu verringern und so den Spalt zu verkleinern, über den die Wäsche beim Übergang von einem Förderband zum anderen springen muss. Das Unterschieben der Wäsche, bei dem diese am Förderband klebt und beginnt, dem Rücklaufband unter dem Förderband zu folgen, kann gelegentlich ein Problem sein. Am besten begegnet man diesem Problem, indem man die Reibung des Bandes möglichst reduziert, sodass sich die Wäsche leicht ablöst. Ist dies nicht möglich, kann man unter der Kopfrolle einen Sensor anbringen, der mit dem Not-Aus des Förderbands verbunden ist und das Förderband stoppt, sobald ein Stück Wäsche versucht, sich entlang des Rücklaufbands zu bewegen.
Sicherheit ist von größter Bedeutung und erfordert häufig den Einsatz von Klemmschutzvorrichtungen am Anfang von Förderbändern. Diese Klemmschutzvorrichtungen können die Ursache für viele Wäschestaus und -klemmen sein, wenn sie nicht korrekt konstruiert sind, d. h. möglichst nahe am Walzenkopf platziert sind und den Belastungen gelegentlicher, unvermeidlicher Staus und der anschließenden Beseitigung standhalten. Wenn ein angetriebenes Förderband auf eine stationäre oder sich langsam bewegende Oberfläche wie einen Tisch oder eine Schwerkraftwalze entlädt, sind Klemmschutzvorrichtungen in der Regel ungeeignet und sollten durch andere Sicherheitssysteme wie elektrische Stoßleisten ersetzt werden, die mit dem Not-Aus-Schaltkreis des Förderbands verbunden sind.
Schutz an der Unterseite des Förderbandes für das Rücklaufband kann durch einen vollflächigen Unterschutz oder lokale Rollenabdeckungen erreicht werden. Beide bieten ein akzeptables Maß an Sicherheit. Bei Förderbändern mit einer Bodenhöhe von weniger als 750 mm sind Rollenabdeckungen oft die bevorzugte Option, da sie eine wirtschaftliche Lösung darstellen, Flusen und andere Ablagerungen auf den Boden fallen lassen und so die Reinigung erleichtern. Zudem ist die Wahrscheinlichkeit, dass Bediener das laufende Band berühren, gering. Förderbänder mit einer Bodenhöhe von 750 mm bis 2500 mm sind oft mit einem vollflächigen Unterschutz ausgestattet, vor allem weil Bediener sich aus psychologischen Gründen nicht gerne neben einem laufenden Band aufhalten – selbst wenn die Fangstellen (Rücklaufrollen) durch Abdeckungen ausreichend geschützt sind.
Bei Bandhöhen über 2500 mm werden fast immer Rollenabdeckungen eingesetzt, da der Kontakt des Bedieners mit dem laufenden Band unwahrscheinlich ist und die Kosten der ausschlaggebende Faktor sind. Darüber hinaus ermöglichen die Rollenabdeckungen dem Wartungspersonal eine einfache Überwachung des Bandzustands, da der größte Teil des Bandes sichtbar ist.