Fothergill Polycom - Fördersystem
Amber Install Overhead-Lösung für den Transport von Gummi
Fothergill Polycom Ltd (ehemals Ferguson Polycom Ltd) produziert und liefert Gummimischungen und gummibeschichtete Gewebe aus einem maßgeschneiderten neuen Werk in Oldham, Lancashire. Das Unternehmen ist der führende Nischenhersteller von kundenspezifischen und branchenüblichen schwarz gefüllten und farbigen Masterbatches und Compounds in Form von Zuschnitten, Endlosplatten und schmalen Streifen. Diese finden Anwendung in einer Vielzahl von Branchen und Verfahren, darunter Formpressen, Spritzgießen, Kalandrieren, Beschichten und Extrudieren.
Fothergill Polycom Ltd. verfügt über ein Archiv mit über 4.000 Rezepturen und entwickelt kontinuierlich Compounds und Masterbatches nach kundenspezifischen Anforderungen und Industriestandards. Typische Anwendungen sind Formteile und Extrusionen im Automobilbereich, Dichtungen für den Einsatz mit Wasser und Gasen, Beschichtungen, Kalandrieren und gehärtete Folien. Sowohl natürliche als auch synthetische Polymere werden in den internen oder offenen Mischern verarbeitet. Das Unternehmen ist flexibel genug, um auch Klein- und Einzelchargenanforderungen zu erfüllen, was sowohl für Entwicklungsarbeiten im kleinen Maßstab als auch für hochspezialisierte Compounds nützlich ist.
Im Rahmen seines laufenden Investitions- und kontinuierlichen Verbesserungsprogramms zog Fothergill Polycom Ltd in neue Räumlichkeiten ganz in der Nähe um. Dabei wurde sichergestellt, dass der Standort für die Belegschaft nicht zu benachteiligen ist und weiterhin eine gute Anbindung an das Straßennetz von Greater Manchester gewährleistet ist.
Amber wurde von Fothergill Polycom mit der Bitte um die Entwicklung einer Methode für den Gummitransport von den Mischern zu den Walzwerken in ihrem neuen Werk in der Drury Lane in Oldham beauftragt. Zuvor wurde hierfür ein Förderband verwendet. Dieses erwies sich jedoch als sehr ineffizient. Der Gummi neigte dazu, über die Bandkanten zu fallen und den Boden zu berühren, was die Wahrscheinlichkeit einer Ausschussware aufgrund von Verunreinigungen erhöhte.
Die starke Neigung des bestehenden Förderbandes führte zudem dazu, dass der Gummi tendenziell zurückfiel, sodass Bediener regelmäßig eingreifen mussten, um den Transportprozess zu unterstützen. Der neue Standort des Mischers bedeutete eine unmittelbare Nähe zum Walzwerk, und der Ablagewinkel des Gummis wäre am neuen Standort noch größer, was eine deutlich größere Herausforderung darstellte.
Ambers Aufgabe im Werk Drury Lane bestand darin, den Gummi von den Mischern zu den Walzwerken zu transportieren, ohne dass der Gummi den Boden berührt, ohne Verschwendung, ohne dass Bediener eingreifen müssen, um den Gummi zu den Walzen zu schieben, und gleichzeitig vollen Zugang zu den Walzen von beiden Seiten zu ermöglichen – und das alles auf wesentlich eingeschränkterem Raum.
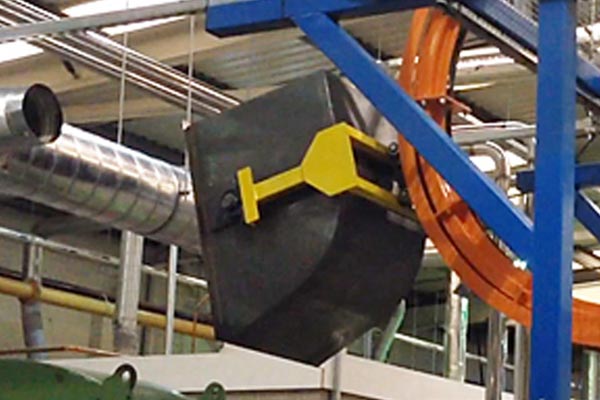
Nach zahlreichen Ideen kam Ambers Industries zu der Lösung, einen Rundkurs mit Standardkomponenten zu schaffen, der aus geraden Schienen, Kurven und Ketten sowie einem Rahmen zur Unterstützung eines Eimers besteht, der so konzipiert ist, dass er unter den Mischer passt, in dem sich der Gummi befindet.
Der Eimer wurde so konstruiert, dass er in horizontaler Position unter dem Mischer verbleibt und bereit zum Beladen ist. Auch während des vertikalen Aufstiegs vor der Fixierung für den vertikalen Kippvorgang wird sichergestellt, dass der Gummi über die Walzwerke ausgeworfen wird. Der Eimer ist außerdem mit Teflon beschichtet, um ein Anhaften des Gummis beim Entladen zu verhindern.