Wehrventile - Hängeförderer
MCM-Hängeförderer bieten eine Lösung für Wehrventile
Als Weir Valves & Controls UK Ltd die Effizienz und Handhabungskapazität ihres Ventillackiersystems durch Kugelstrahlen, eine Lackierkabine und einen Härteofen verbessern wollte, lud das Unternehmen MCM Conveyors aus Oldham ein, ein Angebot für das Projekt abzugeben.
Philip Dollin von Weir Valves & Controls UK Ltd. kommentierte: „Nach Prüfung zahlreicher Ausschreibungen wurde der Spezialist für Hängeförderanlagen MCM Conveyors mit der Bereitstellung einer umfassenden Förderlösung beauftragt. MCM Conveyors war nicht nur wettbewerbsfähig, sondern hat auch deutlich bewiesen, dass das Unternehmen unsere Anforderungen verstanden hat und einen umfassenden Kundendienst bieten konnte, den wir für die Durchführung von Investitionsprojekten als unerlässlich erachten.“
Autotrack 500 Power & Free-Lösung
Das System wurde für maximale Flexibilität und Effizienz bei der Herstellung von Einzelprodukten mit einem Gewicht von bis zu 2.000 kg konzipiert. Diese werden auf maßgeschneiderte, rotierende Mehrvorrichtungs-Flugbalken geladen, die an einem MCM Autotrack 500 (AT500)-Überkopf-„Power + Free“-System aufgehängt sind, um sie auf einem Rundkurs zu bestimmten Entlade-/Endbearbeitungsstationen zu transportieren.
Einzelne Weir-Ventile werden beladen, indem eine hängende Hebe-/Senksteuerung manuell betätigt wird, um den Schlitten auf eine ergonomische Höhe abzusenken, damit Produktschlingen am Ventil befestigt werden können. Jeder Laststangenbaugruppe werden über ein elektronisches Tag verschiedene Daten zugewiesen, die in den Kabinen- und Ofenbereichen verwendet werden, um Produktverlauf, Lackierung und Aushärtezeiten zu bestimmen. Sobald die Schlingen sicher befestigt und das Ventil abgedeckt sind, beginnt der Bediener, den Schlitten des Fallabschnitts auf die letzten 200 mm anzuheben. Anschließend wird die vertikale Bewegung automatisch durch eine SPS abgeschlossen, die alle Steuerungen und Bewegungen innerhalb des Systems überwacht. Ein Entriegelungsknopf aktiviert und gibt die Laststange frei, um das Ventil zu transportieren und es am Strahleingang zu sammeln, sodass eine leere Laststangenbaugruppe in die Be-/Entladestation einfahren kann.
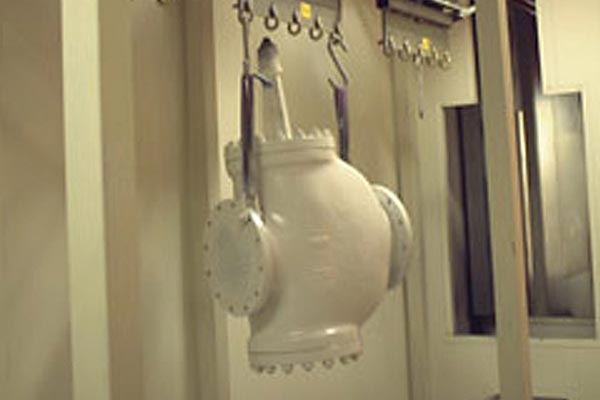
Aus Sicherheitsgründen wurde eine Produktladeklappe eingebaut, um zu erkennen, dass der Arbeitsbereich nicht überschritten wird. Bei der Beladung eines übergroßen oder falsch ausgerichteten Produkts löst das Förderband einen Alarm aus und stoppt. Die Ladebalkenbaugruppe fährt in die Einhausung ein, sobald die SPS eine leere Position erkennt und ein Mitarbeiter die Produktabruftaste betätigt. Nach Abschluss des Strahlvorgangs betätigt der Strahler die Produktfreigabetaste, um die Maschinentüren automatisch zu öffnen und das Produkt zur Lackierkabine zu transportieren.
Nach dem gleichen Eingangsvorgang wird der Multi-Jig-Mitnehmer in der Lackierkabine automatisch per Druckknopf entriegelt und ermöglicht dem Bediener, das Produkt während des Lackierens zu drehen. Nach Abschluss des Lackiervorgangs wird der Mitnehmer wieder in seiner Inline-Position auf dem MCM-Hängeförderband verriegelt. Als Vorsichtsmaßnahme ist eine spezielle Führung angebracht, um den rotierenden Mitnehmer neu auszurichten und zu verriegeln, falls der Bediener den Vorgang übersehen hat. Sollte der Mitnehmer jedoch aus irgendeinem Grund über einen zulässigen Winkel hinaus verstellt sein, erkennt ein Ladetor die Position, löst automatisch einen Alarm aus und stoppt das Förderband.
Mithilfe des elektronischen Lese-/Schreibsystems liefert das Steuerungssystem den Mitarbeitern automatisch Prozessinformationen wie Lackfarbe, Anzahl der Lackschichten und Aushärtezeiten. Das Lese-/Schreibsystem ermöglicht zudem das Hinzufügen zusätzlicher Informationen zu einzelnen Lastbalken durch Weir Valves & Controls. Alle Bedienelemente und Aktivierungstasten innerhalb der Kabinengehäuse sind eigensicher.
Nachdem die Ventile die Lackierkabine verlassen haben, sammeln sie sich in einer Reihe auf dem MCM-Hängeförderband. Eine Weichensteuerung erkennt die Aushärtezeiten (3 oder 6 Stunden) und sortiert die Produkte auf verschiedene Förderbänder, um sie durch den Ofen zu leiten. Beim Verlassen des Ofens werden die Produkte zu einer Linie zusammengeführt und entweder für eine Mehrfachlackierung wieder in den Kreislauf zurückgeführt oder automatisch zur Be-/Entladestation geleitet, um dort auf eine bereitstehende Palette abgesenkt zu werden. Der leere Förderbalken wird anschließend erneut mit Produkt beladen, um den Lackierzyklus erneut zu starten.
Das System wurde erfolgreich installiert und läuft störungsfrei. Weir Valves & Controls UK berichtet: „MCM Conveyors arbeitete eng mit unserem Projektteam zusammen, und wir haben eine gute Zusammenarbeit entwickelt. Das Engagement von MCM bei der Umsetzung dieses Projekts war einwandfrei, und die Installation wurde termingerecht und im Rahmen des Budgets abgeschlossen. Nach der Installation schulte MCM unsere Mitarbeiter und erläuterte grundlegende Wartungsabläufe. Wichtig war, dass die Linie maximale Flexibilität bot, um die Ventillackierung nach den individuellen Kundenanforderungen durchführen zu können. Das System läuft seit seiner Installation erfolgreich und zuverlässig, und Weir Valves & Controls UK beauftragte MCM mit der Bereitstellung eines fortlaufenden Service- und Wartungspakets. Aufgrund dieses Erfolgs und der oben genannten Erfahrungen kann ich MCM uneingeschränkt empfehlen.“