SEW Eurodrive - Hängeförderer
Automatisiertes Fördersystem für SEW Eurodrive
SEW Eurodrive ist weltweit als Marktführer im Bereich Antriebstechnik anerkannt, ist auf fünf Kontinenten vertreten und beschäftigt 14.000 Mitarbeiter. Bei der Planung der neuen Produktionsstätte in Normanton, West Yorkshire, erkannte SEW die Chance, ein automatisiertes Fördersystem für die neue Lackieranlage einzuführen und so die bestehenden Prozesse für die Antriebstechnik zu optimieren.
In enger Zusammenarbeit mit den Ingenieuren von SEW Eurodrive entwickelte Amber Industries Ltd eine schlüsselfertige Lösung und erhielt anschließend den Auftrag für das neue Fördersystem unter Verwendung unseres standardmäßigen Autotrack 500M Power & Free-Hängeförderers.
Die Vorgabe von Sew Eurodrive bestand darin, dass das Förderband alle Getriebemotoren von 15 kg bis 1000 kg bewältigen musste. Diese Einheiten wurden an einem Ende der Fabrik beladen. Das System sollte die Möglichkeit bieten, Produkte vom Tagesgeschäft abzuzweigen und über farbige Bahnen sowie eine „Fast-Track-Bahn“ zu verfügen. Diese Schnellbahn, die das normale Tagesgeschäft umgeht, ist für SEW sehr wichtig, da das Unternehmen stolz auf seinen Service ist, Kunden auch bei Eillieferungen beliefern zu können.
Außerdem musste das Förderband das Produkt in der Spritzkabine und im Inspektionsbereich anheben und absenken können, während der Bediener die Einheit während des Spritzvorgangs drehen konnte. Ein mehrstufiger Fallabschnitt im Inspektionsbereich ermöglichte dem Bediener eine gründliche Prüfung des Produkts vor dem Versand an die entsprechenden Entladestationen.
Um alle SEW-Anforderungen zu erfüllen, wurde das System mit zwei Ladestationen mit einer stationären Trolley-Set-Baugruppe ausgestattet, die es dem Bediener ermöglicht, das Produkt an den Stützpunkten der Trolley-Laststange zu befestigen. Kleinere Produkte werden dabei an einer der Rotationseinheiten der Laststange aufgehängt, während größere Produkte am zentralen Rotationspunkt aufgehängt werden.
Der Bediener an einer der beiden Ladestationen scannt das/die Produkt(e) und drückt dann an seinem Arbeitsplatz eine Taste, die bestimmt, ob der beladene Einkaufswagen zum normalen Geschäfts-, Farb- oder Fast Track-Bereich weitergeleitet werden soll.
Wenn der Wagen die Lagergasse erreicht, leitet die Förderweiche den Wagen automatisch in die entsprechende Lagergasse um.
Ein Monitor in der Lackierkabine ermöglicht dem Bediener, die anstehenden Aufträge einzusehen und die entsprechende Spur auszuwählen. Die Fast Track-Spur umgeht das sich ansammelnde Tagesgeschäft, sodass die Anlage ohne Unterbrechung durch den normalen Betrieb lackiert werden kann.
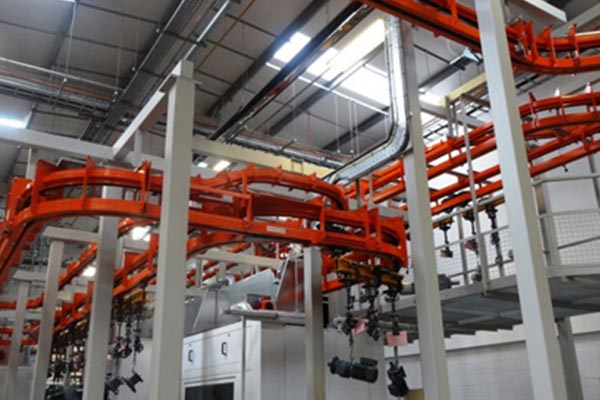
Wenn sich der Wagen nun in der Spritzkabine befindet, kann der Bediener den Fallabschnitt je nach Bedarf auf eine ergonomische Höhe absenken, um alle relevanten Aspekte des Produkts spritzen zu können, während er stationär bleibt.
Die Laststangenanordnung wurde so konzipiert, dass die Produkte während des Sprühvorgangs um 360 Grad gedreht und nach dem Sprühvorgang arretiert werden können, um die korrekte Produktausrichtung beizubehalten. Ein wesentlicher Vorteil des Fallabschnitts besteht darin, dass das Absenken des Produkts im Vergleich zu einem herkömmlichen Förderband auf und ab auf einem kleinen Bereich erfolgen kann.
Nachdem der Farbsprühvorgang abgeschlossen ist und sich der Absenkabschnitt in der angehobenen und verriegelten Position befindet, drückt der Bediener erneut eine Taste, die erneut bestimmt, ob die Produktroute der des normalen Tagesgeschäfts oder die Trolleyroute der „Schnellstrecke“ entspricht.
Der Wagensatz mit dem lackierten Produkt wird automatisch wieder in das System freigegeben, wo es im Trockenofen für eine festgelegte Zeit und Temperatur trocknet. Die Produkte werden dann automatisch gesammelt und aus dem Trockner freigegeben, sobald sie die festgelegte Zeit im Ofen verbracht haben.
Da die gesamte Lackieranlage in bestimmten Teilen der Anlage über automatisch öffnende Türen verfügt, müssen die elektronischen Steuerungen des Fördersystems mit diesen Elementen synchronisiert werden, um Kollisionen beim Öffnen und Schließen zu vermeiden.
Anschließend wird das Produkt zum Haupttrocknungsofen geleitet, wo es erneut für eine andere festgelegte Zeit und Temperatur im Ofen gespeichert wird.
Beim Verlassen der Hauptaushärtung wird der Wagensatz mit dem getrockneten Produkt dann automatisch entweder in die normale Geschäftslinie umgeleitet oder auf die „Überholspur“ geleitet.
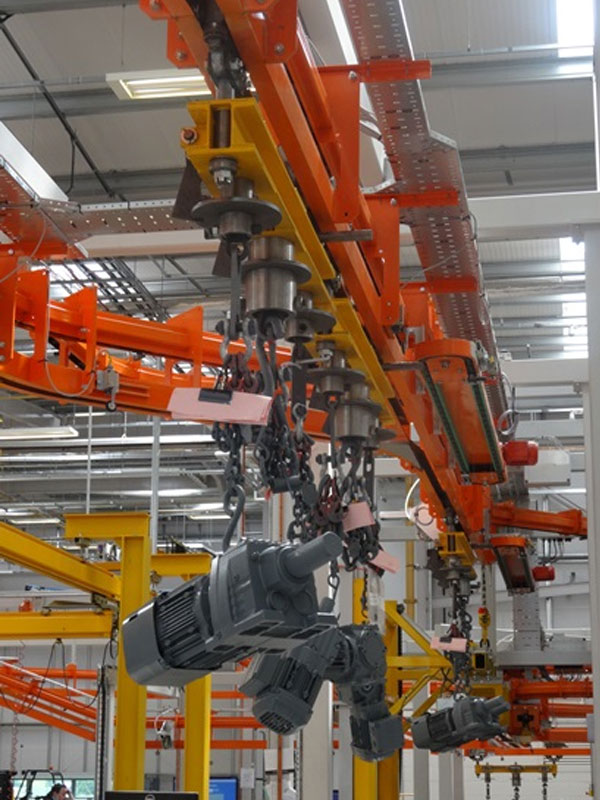
Produkte, die für das tägliche Geschäft bestimmt sind, werden in eine Lagerschleife umgeleitet, die dann weiter zum mehrstufigen Inspektionsabwurfbereich fährt. Trolley-Sets, die als Fast Track (dringende Bestellungen) gelten, gelangen jedoch nicht in die normale Geschäftsschleife, sondern werden direkt zum Inspektionsabwurfbereich umgeleitet. Das beladene Trolley-Set bleibt für den Inspektionsprozess wieder stationär, sodass der Bediener das Produkt anheben und absenken sowie um 360 Grad drehen kann, um eine vollständige Inspektion zu gewährleisten.
Nach Abschluss der Inspektion entscheidet der Bediener, ob das Produkt zur Entladestation 1 oder 2 transportiert werden soll. Die geprüfte Einheit wird nun automatisch zum gewünschten Entladeziel geleitet. Nach dem Entladen werden die leeren Wagensätze zurück zu den Ladestationen geleitet. Modernste Elektronik ermöglicht die Integration des Fördersystems in andere Anlagen und Geräte und gewährleistet so die korrekte Produktbewegung und -taktung bei Bedarf. Auch die Stellen, an denen die Produkte über die Laufstege transportiert werden, mussten berücksichtigt werden. Angesichts dessen und der damit verbundenen Gewichte wurde bei Bedarf ein robuster, begehbarer Unterbodenschutz angebracht.