Sandvik-Lackieranlage – Förderband
Sandvik Lackieranlagen-Förderband
Seit fast 150 Jahren steht der Name Sandvik für Qualität. Das Unternehmen erzielt einen Jahresumsatz von 89 Milliarden Schwedischen Kronen und beschäftigt weltweit 47.000 Mitarbeiter. Das Sandvik-Werk für Bau und Bergbau in Ballygawley, County Tyrone, ist heute das Kompetenzzentrum für die Herstellung mobiler Brech- und Siebanlagen für den weltweiten Einsatz in der Bergbau- und Steinbruchindustrie.
Im Zuge der geplanten Erweiterung der aktuellen Produktionsanlage in Ballygawley erkannte Sandvik, dass Bedarf an einer neuen Endbearbeitungsanlage bestand, die Strahlkabinen, Lackierkabinen, Öfen und ein automatisiertes Fördersystem umfassen würde, um diesen Teil des Produktionsprozesses zu rationalisieren und der ständig steigenden Nachfrage nach Maschinen gerecht zu werden.
In enger Zusammenarbeit mit den Ingenieuren von Sandvik und anderen beteiligten Großauftragnehmern entwickelte Amber Industries Ltd eine schlüsselfertige Lösung und erhielt anschließend den Auftrag für das neue Fördersystem unter Verwendung unseres standardmäßigen Autotrack 500M Power & Free-Hängeförderers.
Die Anforderungen
Sandviks Vorgabe war, dass das Fördersystem alle Brecher- und Siebkomponenten mit einem Gewicht von bis zu 3000 kg und einer Länge von ca. 8000 mm bewältigen musste. Eine Hauptanforderung an das Fördersystem war die einfache Be- und Entladung dieser langen und schweren Komponenten. Nach der sicheren Beladung sollten die Komponenten automatisch durch verschiedene Anlagen und Geräte transportiert werden. Dabei musste das Fördersystem zeitweise stillstehen, während sich das Produkt in anderen Prozessbereichen kontinuierlich bewegte.
Um alle Anforderungen von Sandvik zu erfüllen, wurde das System mit zwei 9000 mm langen Absenkstrecken konzipiert, eine im Lade- und eine im Entladebereich. Die Ladestation verfügt über eine stationäre, leere Mitnehmerbaugruppe, die es dem Bediener ermöglicht, die Mitnehmer auf dem Absenkstreckenwagen, der die Förderbahn aufnimmt, auf eine ergonomisch geeignete Ladehöhe abzusenken.
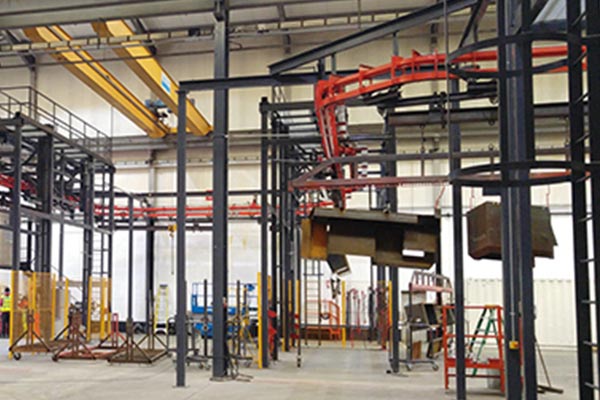
Anschließend werden die Stangen und das Produkt von der schneller laufenden Lieferkette auf eine langsamer laufende Prozesskette übertragen, wo das Produkt kontinuierlich in einem vorgegebenen Abstand durch eine Grundierungskabine und anschließend für eine festgelegte Zeit und Temperatur durch einen Grünhärtungsofen läuft.
Nach der Grünhärtung und dem Ablüften wird die Deckschicht in einer zweiten Pulverbeschichtungskabine aufgetragen, die wiederum durch den Haupthärtungsofen läuft, um dort bei einer Temperatur von 220 Grad Celsius für einen festgelegten Zeitraum endgültig auszuhärten.
Als Teil des Systems ist das Förderband mit einer Produktionsstoppeinrichtung ausgestattet, die über ein Ampelsignal verfügt, das anzeigt, ob das Förderband zu Produktionszwecken oder als Notstopp angehalten wurde.
Mit dieser Einrichtung können Bediener das Prozessförderband stoppen, während das Lieferförderband (Schnellkette) weiterläuft. Dadurch können die Entladevorgänge effektiv aufrechterhalten werden, ohne dass die gesamte Anlage angehalten werden muss.
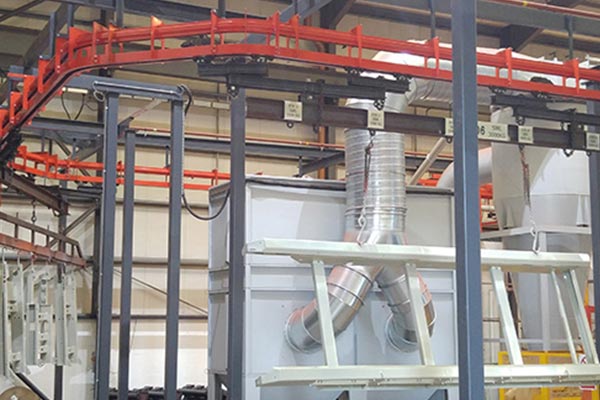
Das Entladen des Produkts erfolgt ebenso wie das Beladen über eine zweite, 9000 mm lange Fallstrecke, die es den Bedienern ermöglicht, das stationäre, fertig lackierte Produkt auf eine geeignete Entladehöhe abzusenken. Nach der Entnahme des Produkts steigt der leere Mitnehmer wieder auf ein höheres Niveau an und wird zurück zur Ladefallstrecke transportiert. An den Fallstrecken sind Sperrtore angebracht, um eine sichere Entnahme des Produkts zu gewährleisten. Ein wesentlicher Vorteil der Fallstrecken besteht darin, dass das Absenken des Produkts im Vergleich zu einem herkömmlichen Förderband mit Auf- und Abwärtsbewegung auf einem kleinen Bereich erfolgen kann. Die Tatsache, dass der stationäre Mitnehmer auf geeignete Be- und Entladehöhen abgesenkt werden kann, erweist sich für die Bediener als Vorteil, da dies den unterschiedlichen Produktgrößen gerecht wird.
Der Einsatz modernster Elektronik ermöglicht die Integration des Fördersystems in andere Anlagen und Geräte und gewährleistet so die korrekte Produktbewegung und -steuerung bei Bedarf. Die Hauptsteuerung ist mit einer Fernzugriffsfunktion ausgestattet, die es den Softwareentwicklern von Amber Industries Ltd. ermöglicht, von unserem Produktionsstandort in Oldham, Lancashire, auf das System zuzugreifen.
